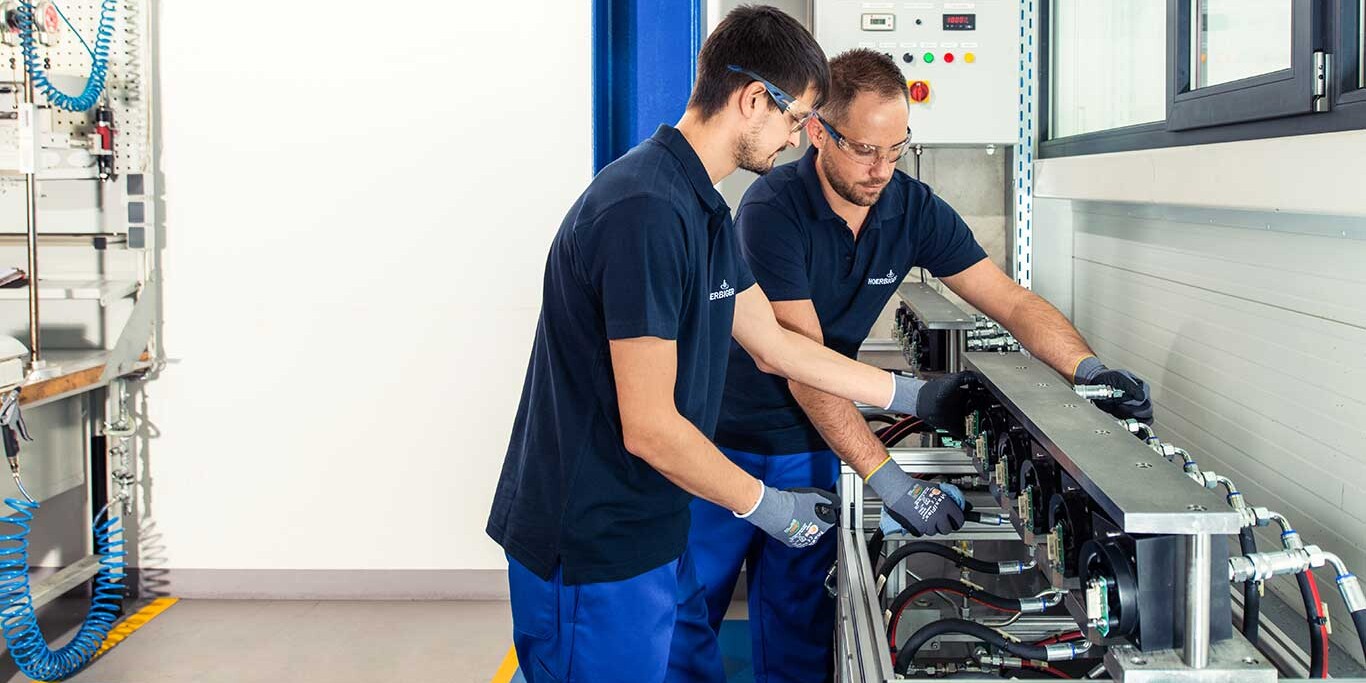
HydroCOM Service
Stepless Capacity Control System
Inspection, minor or major service of all product variants of
HOERBIGER’s HydroCOM – Stepless Capacity Control System
Testing, inspection, minor repair in HOERBIGER workshops or major repair on-site directly in the field. With our proven and standardized offering you will find the reconditioning service that best suits you and your HydroCOM system.
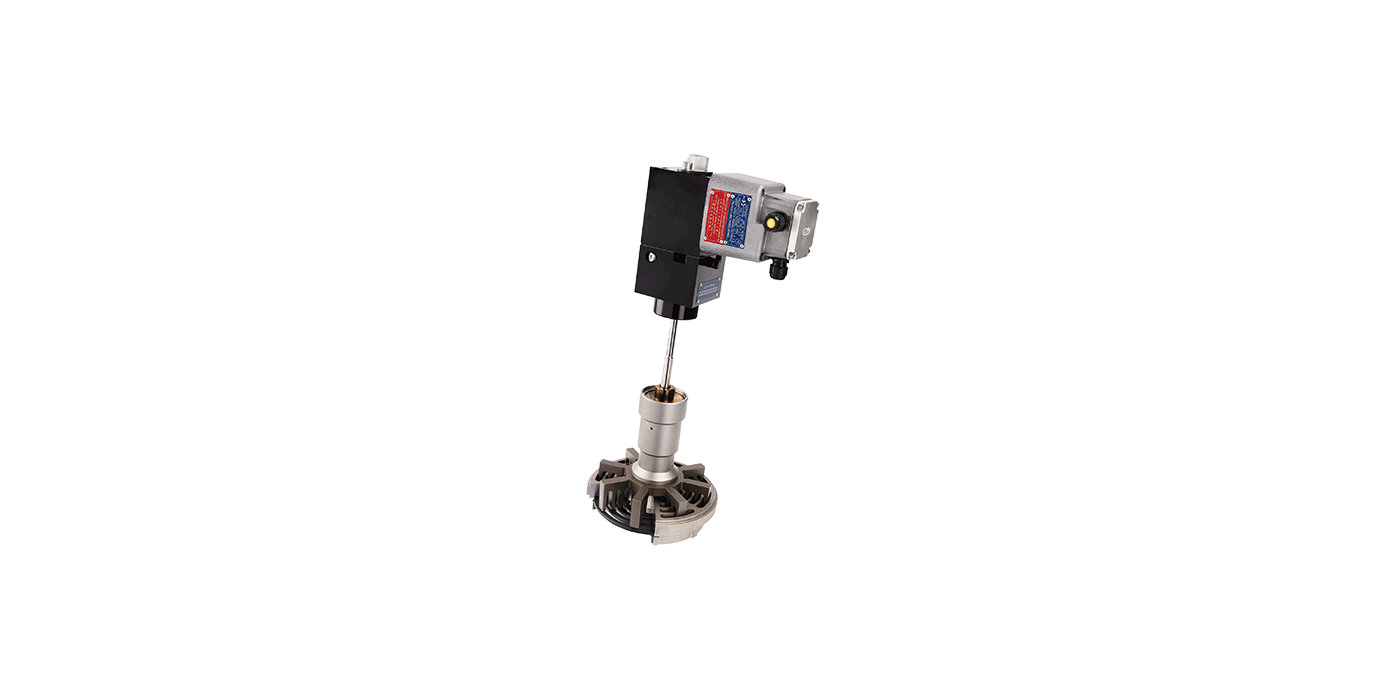
HydroCOM is stepless and fully automated capacity control system for reciprocating compressors. Due to the high reliablity of the system, long maintenance intervals assure high availability. However, the HydroCOM system must be serviced at the recommended maintenance intervals. This ensures longer lifetime and avoid unplanned downtime.
Services at a glance
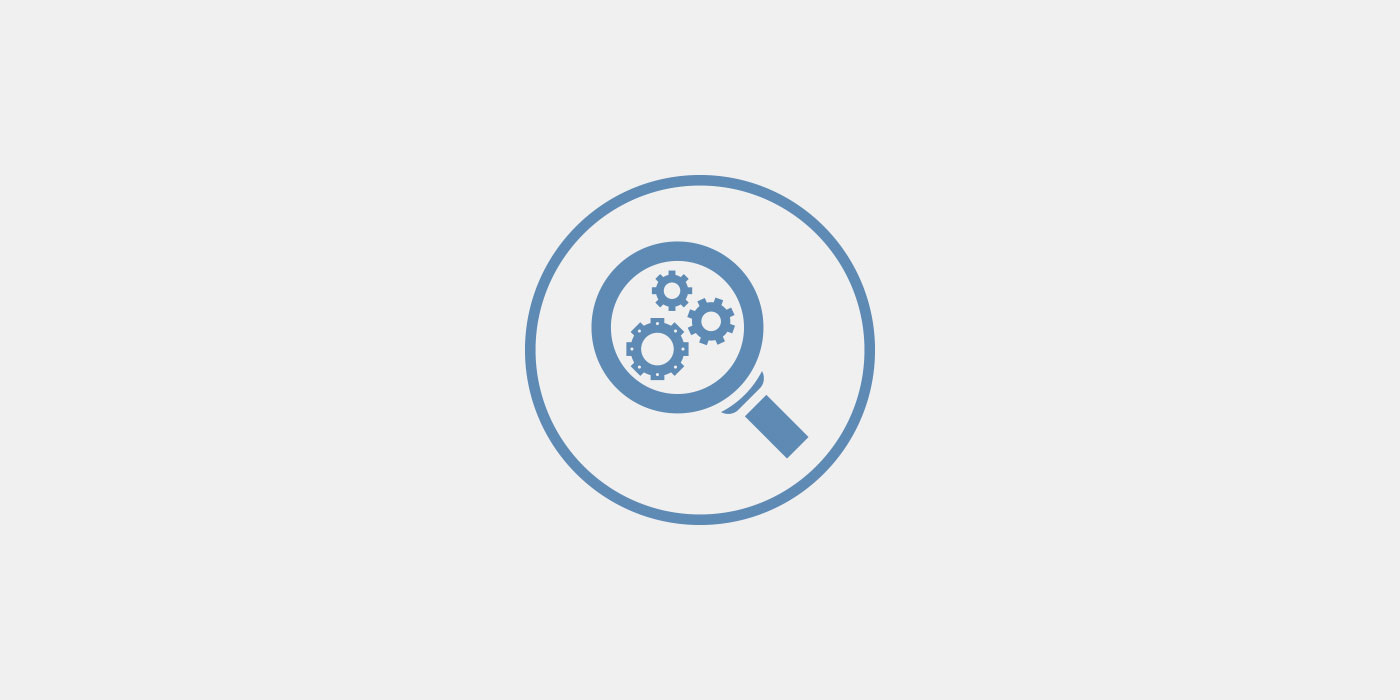
- Electric housing: Inspection and repair kit
- Valve housing: Inspection, cleaning and repair kit
- Seal housing: Inspection
- Inspection report
Maximum runtime 16,000 hrs
- Electric housing: Inspection and repair kit
- Valve housing: Inspection, cleaning and repair kit
- Seal housing: Inspection and replacement of sealing cartridges
- Hydraulic unit: Inspection, exchange filter and hydraulic oil
- Repair report
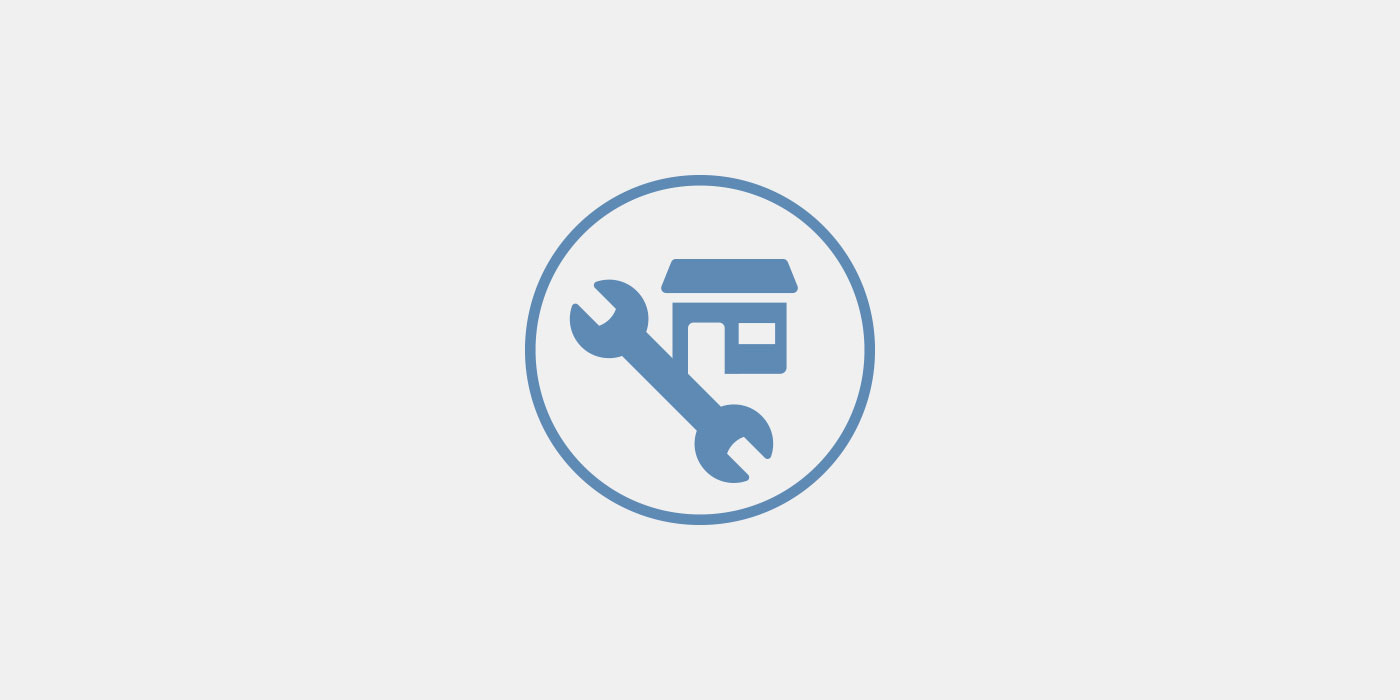
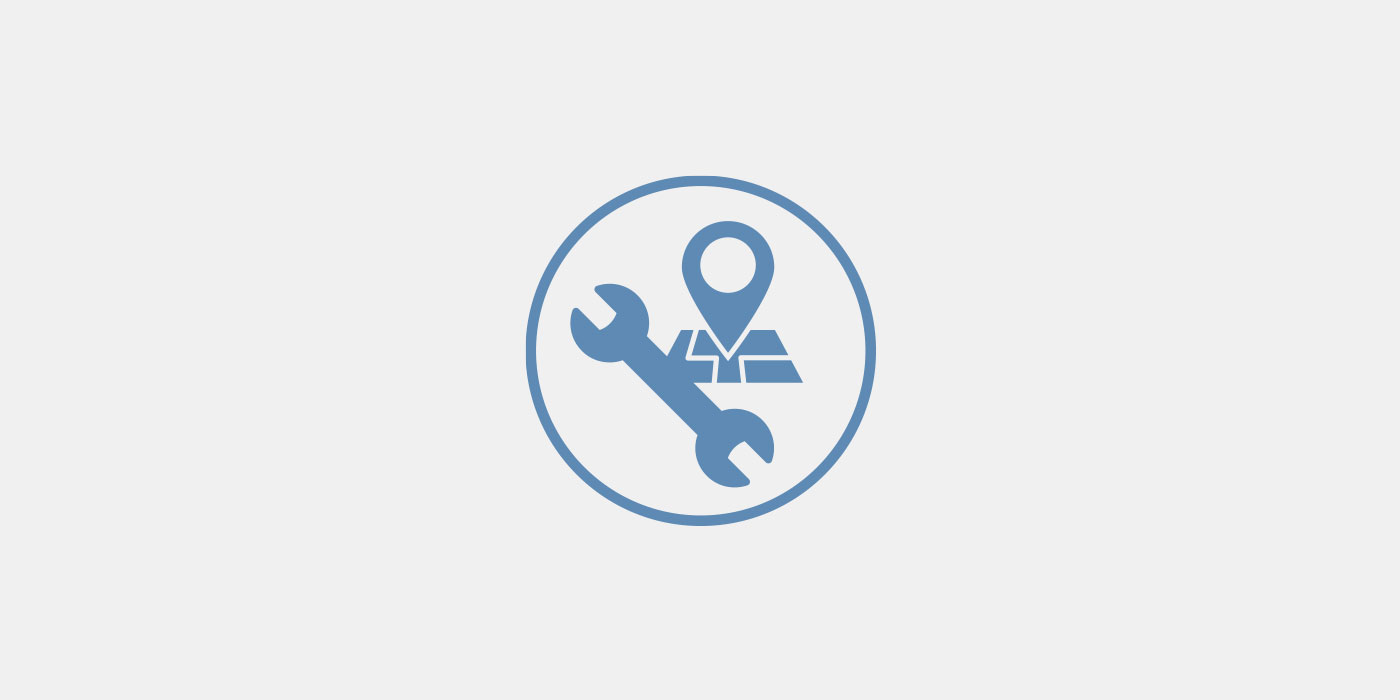
Maximum runtime 40,000 hrs
- Electric housing: Inspection and repair kit
- Valve housing: Exchange
- Seal housing: Inspection and replacement of sealing cartridges
- Hydraulic unit: Inspection, exchange filter and hydraulic oil, exchange pump and coupling
- Visual inspection of electric cabling and hydraulic piping
- Repair report
Planning is everything – combine maintenance with scheduled downtime
Time is money, yet often the HydroCOM System Service does not coincide with planned compressor downtime. That increases time, effort, costs, and significantly reduces performance due to multiple shutdowns. It is therefore only understandable that the service intervals are reluctantly adhered to, but this can cause considerable damage in the long run. However, HOERBIGER provides a solution for every challenge. Now, though, these issues belong to the past. We have speeded up the service process for you by relocating all HydroCOM service-related activities from the workshop directly to the compressor in the field – coordinated with your planned shutdowns, of course.
All-around carefree – your benefits of our on-site service
- No need to receive components into HOERBIGER workshop for major service
- Field sales technician has the new and tested valve housing and sealing cartridges for replacement
- Dry run/ actuator test/ simulation
- Purging of hydraulic system
- Adjusting hydraulic pressure
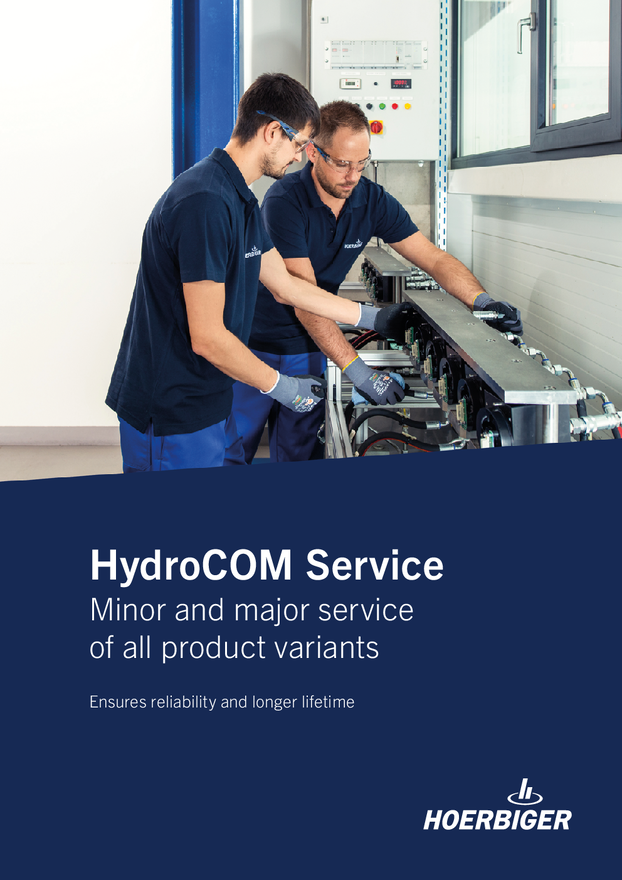
Brochure A4 Format
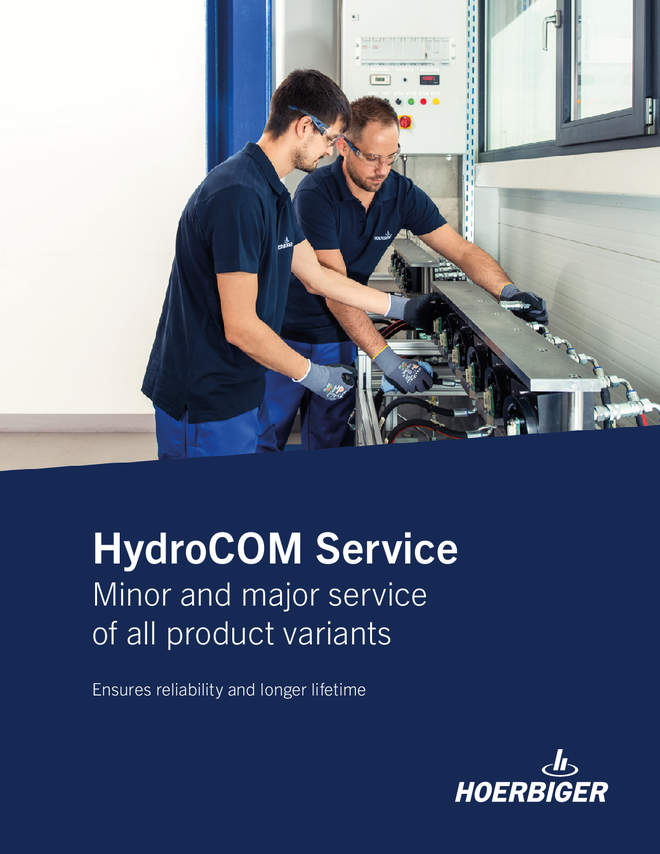
Brochure Letter Format
How can we help you?
Let us know if you need assistance or have questions – one of our compression representatives will contact you as soon as possible.
Don’t miss out on the latest news!
Sign up below to receive the latest news and updates from HOERBIGER about our compression products and services.